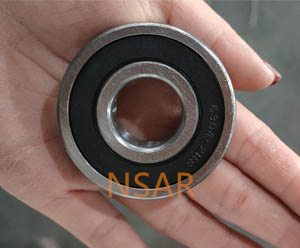
Deep groove ball bearings are essential components in a wide range of mechanical systems, from automotive engines to industrial machinery. Their ability to enable smooth, low-friction rotation while accommodating radial and limited axial loads makes them indispensable in various applications.
However, to fully harness their potential and tailor them to meet the specific demands of different industries, engineers often contemplate the implementation of preload—a controlled axial force applied to these bearings.
This comprehensive exploration dives deep into the significance of preload in deep groove ball bearings, scrutinizing when and why it is essential, the numerous methods available for its application, and the associated challenges.
By gaining a deep understanding of preload in these bearings, engineers and designers can optimize performance, enhance system rigidity, and prolong the lifespan of critical rotating components.
Understanding Deep Groove Ball Bearings
Deep groove ball bearings are fundamental components of mechanical engineering, celebrated for their versatility and efficiency. They feature a simple yet effective design, comprising an outer ring (outer race), an inner ring (inner race), a set of rolling elements typically in the form of balls, and a cage to maintain spacing between the balls.
This basic structure enables deep groove ball bearings to excel in myriad applications, from household appliances to heavy industrial machinery.
One of their primary features is the ability to handle radial loads, which act perpendicular to the shaft’s axis, making them suitable for supporting radial loads in various systems. Furthermore, deep groove ball bearings can also accommodate limited axial loads (thrust loads) in both directions, further enhancing their utility.
A crucial aspect of deep groove ball bearing operation is bearing clearance, which refers to the internal gap between the rolling elements and the raceways within the bearing.
This clearance is vital to prevent overheating and ensure smooth rotation.
However, maintaining a delicate balance between adequate clearance and minimizing it to enhance bearing stiffness is a crucial consideration, especially in applications where precision and rigidity are critical.
Understanding the construction and operation of deep groove ball bearings lays the foundation for comprehending the role and necessity of preload.
Concept of Preload in Bearings
Preload is a critical concept in the realm of bearings, including deep groove ball bearings. It refers to the intentional application of a controlled axial load along the shaft’s axis before a bearing enters into service.
This axial force eliminates or minimizes the internal clearance within the bearing, ensuring that the bearing elements (balls or rollers) are in constant contact with the raceways. The primary objectives of introducing preload into bearings are as follows:
1.Minimize Internal Clearance: Preload serves to eradicate or significantly reduce the internal clearance within the bearing. This eradication of play between the bearing components results in heightened stiffness and reduced vibration, making it particularly advantageous in applications where precision and stability are paramount. In essence, preload ensures that there is no slack within the bearing, which is crucial for precise and repeatable motion.
2.Enhance Rigidity: By applying a controlled axial force, preload increases the bearing’s resistance to external forces and moments. This heightened rigidity is essential in applications where any deflection or misalignment must be minimized, such as in machine tools or robotic systems.
3.Improving Axial Load Capacity: In addition to its role in eliminating internal clearance, preload can enhance a bearing’s ability to withstand axial loads (thrust loads). This feature is especially valuable in applications where axial loads are substantial and need to be efficiently managed. In summary, preload transforms a bearing from a flexible element with internal clearance into a rigid and precise component that excels in maintaining accurate positioning, minimizing vibration, and enhancing load-carrying capacity. The decision to employ preload hinges on the specific requirements of the application and its critical performance parameters.
When is Preload Needed in Deep Groove Ball Bearings?
Preload in deep groove ball bearings is needed in specific scenarios where the application demands enhanced precision, rigidity, and axial load capacity. Here are the key situations when preload becomes essential:
1.High-Precision Applications: In applications requiring utmost accuracy, such as machine tool spindles, measuring instruments, or optical devices, preload is often indispensable. It eliminates any internal clearance, ensuring that the bearing operates with minimal play, resulting in precise and repeatable motion.
2.Vibration-Sensitive Systems: Preload plays a crucial role in reducing vibration in rotating systems. Industries like aerospace, medical devices, and semiconductor manufacturing rely on the elimination of bearing play through preload to achieve smoother operation and maintain high product quality.
3.Rigidity-Critical Systems: When the application demands minimal deflection or misalignment, preload is beneficial. For example, in robotics and industrial automation, preloaded bearings are used to maintain system rigidity, accuracy, and repeatability in movements.
4.High Axial Load Applications: Deep groove ball bearings are primarily designed for radial loads, but they can tolerate limited axial loads.
In applications where significant axial loads are present, introducing preload can significantly enhance the bearing’s ability to withstand these forces, thus extending its operational lifespan.
In essence, preload is employed to tailor deep groove ball bearings to the specific requirements of precision, rigidity, vibration control, and axial load management in diverse mechanical systems. Its necessity arises when achieving these performance attributes is paramount for the successful operation of the application.
Achieving Preload in Deep Groove Ball Bearings
Implementing preload in deep groove ball bearings involves the deliberate application of a controlled axial force to eliminate internal clearance and ensure that the bearing elements maintain contact with the raceways.
Achieving this preload requires careful consideration and the use of various methods, depending on the application’s specific requirements. Here are the primary methods for introducing preload in deep groove ball bearings:
Spring Preload:
. Wave Springs: These flat wire springs are positioned between bearing components to create a controlled axial force. They offer precise control of preload and are relatively easy to install.
. Belleville Washers: Also known as conical spring washers, Belleville washers provide preload by compressing when subjected to axial load. They are commonly used in pairs to achieve the desired preload magnitude.
Spacer Rings:
. Using spacer rings between the inner and outer bearing races can create preload. The thickness and material of the spacer determine the amount of preload generated. This method is simple and cost-effective but requires accurate sizing and positioning of spacers.
Axial Adjustments:
. Some deep groove ball bearings are designed with axial adjustment features, allowing precise control of preload by adjusting the position of the inner or outer ring along the shaft. This method offers versatility but requires careful adjustment during installation.
Angular Contact Bearings:
. Angular contact ball bearings inherently introduce some degree of preload due to the contact angle of their raceways. They are suitable for applications where both radial and axial loads are significant. The choice of preload method depends on the specific application’s requirements, load conditions, and the desired level of precision. Engineers must carefully assess these factors to select the most appropriate method and achieve the desired performance characteristics in deep groove ball bearings.
Considerations and Challenges in Preloading Deep Groove Ball Bearings
The implementation of preload in deep groove ball bearings brings forth several critical considerations and challenges that engineers and designers must navigate:
1. Overloading Risk: Excessive preload can lead to overloading of the bearing, resulting in premature wear and potential failure. It is imperative to perform meticulous engineering calculations and testing to determine the optimal preload force that balances rigidity with bearing longevity.
2. Temperature Effects: The introduction of preload can generate additional heat within the bearing due to increased friction. Proper lubrication and monitoring of bearing temperature are essential to prevent overheating, which can lead to reduced bearing life.
3. Tolerance and Fit: Achieving the desired preload magnitude necessitates precise control over tolerances and fits, both within the bearing and its associated components. Preload applications may require tighter tolerances, increasing manufacturing complexity and cost.
4. Installation and Maintenance: Proper installation techniques and ongoing maintenance are crucial for maintaining preload over the bearing’s service life. Careful handling during installation and regular inspections are imperative to ensure optimal performance.
5. Balancing Performance: Achieving the right balance between preload and clearance is challenging. While preload enhances rigidity and accuracy, excessive preload may compromise bearing longevity and lead to increased friction and wear.
6. Variability in Load Conditions: Load conditions in real-world applications can vary significantly. Designing for preload must consider these variations to ensure the bearing performs effectively under different operating conditions.
Addressing these considerations and challenges requires a deep understanding of bearing mechanics, rigorous engineering analysis, and a commitment to ongoing maintenance and monitoring to ensure the successful implementation of preload in deep groove ball bearings.
Preload Calculation and Engineering Analysis in Deep Groove Ball Bearings
Preload calculation and engineering analysis are pivotal aspects of optimizing the performance of deep groove ball bearings when preload is a necessity.
This process involves precise calculations and assessments to determine the appropriate preload force for a given application. Here are the key elements of preload calculation and engineering analysis:
1. Load Analysis: Engineers must thoroughly analyze the expected loads, both radial and axial, that the bearing will encounter during operation. Understanding the load distribution is critical in determining the ideal preload magnitude.
2. Bearing Geometry: Detailed examination of the bearing’s geometry, including the dimensions of the inner and outer races, the number and size of balls, and the contact angles, is crucial for preload calculation.
3. Clearance Measurement: Measuring the initial internal clearance in the bearing is essential. This baseline data serves as a starting point for preload calculations.
4. Material Properties: Consideration of material properties, such as the modulus of elasticity and coefficient of friction, plays a role in the engineering analysis.
5. Lubrication: The type and quality of lubrication must be factored in, as it impacts friction and heat generation within the bearing.
6. Finite Element Analysis (FEA): Numerical simulation techniques, including FEA, are often employed to model and analyze the behaviour of the bearing under various preload conditions.
7. Prototyping and Testing: Physical prototypes may be constructed to validate the preload design, and testing is conducted to ensure that the calculated preload force aligns with the desired performance characteristics. Balancing the need for rigidity with bearing longevity and performance under variable load conditions is the primary goal of preload calculation and engineering analysis. It requires a combination of theoretical calculations, simulation tools, and practical testing to achieve the desired results in deep groove ball bearings.
Conclusion:
In conclusion, deep groove ball bearings play an integral role in countless mechanical systems, offering efficiency and versatility. However, to optimize their performance and adapt them to the specific demands of different industries, engineers often turn to preload—a controlled axial force applied to these bearings.
This exploration has delved into the significance of preload in deep groove ball bearings, examining when and why it becomes indispensable, the numerous methods for introducing it, and the associated challenges. By gaining a deep understanding of preload’s intricacies, engineers and designers can unlock the potential for enhanced performance, increased system rigidity, and extended bearing lifespans in critical rotating components.
FAQs:
What is preloaded in deep groove ball bearings?
Preload in deep groove ball bearings refers to the intentional application of a controlled axial load to eliminate or minimize internal clearance within the bearing. It enhances bearing stiffness, reduces vibration, and improves load-carrying capacity.
When is preload necessary in deep groove ball bearings?
Preload is needed in situations where applications require enhanced precision, rigidity, reduced vibration, or improved axial load capacity. It is commonly used in high-precision machinery, vibration-sensitive systems, rigidity-critical applications, and when dealing with significant axial loads.
What methods are used to achieve preload in deep groove ball bearings?
There are several methods to introduce preload in deep groove ball bearings, including spring preload (using wave springs or Belleville washers), spacer rings, axial adjustments, and the use of angular contact bearings. The choice of method depends on the specific application’s requirements and load conditions.