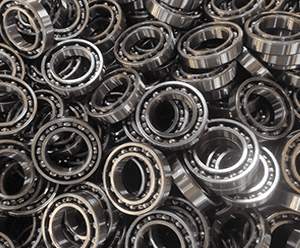
Introduction to Deep Groove Ball Bearings
Deep groove ball bearings, often referred to as radial ball bearings, are a type of rolling element bearing designed to handle primarily radial and axial loads. These bearings feature deep, uninterrupted raceway grooves on inner and outer rings, allowing the balls to move smoothly within them. This design enables deep groove ball bearings to support a wide range of loads, making them a popular choice in various applications.
Design and Components
Ball bearings with deep grooves are crucial parts of many mechanical systems. They consist of several key components that work together to facilitate smooth and reliable rotation:
1.Inner and Outer Rings: Deep groove ball bearings normally feature two rings, one inner and one outer. These rings are commonly made from high-quality steel or other materials, depending on the application’s thorough needs. The inner ring holds onto the shaft, while the outer ring is scaled in a lodging. These rings have precision-machined raceway grooves to show the direction of the balls.
2.Balls: The balls in a deep groove ball bearing come in different materials, including steel, ceramic, and hybrid materials. Steel balls are the most typical alternative due to their affordability and durability. Ceramic balls are used in high-performance applications where diminished importance and improved speed are important. Hybrid bearings incorporate steel coils with ceramic balls, showing a balance between durability and implementation.
3.Cages: Cages, also known as retainers, are used in deep groove ball bearings to keep the balls evenly spaced and prevent them from touching each other. This spacing is essential to reduce friction and wear. Common materials for cages include steel, brass, and synthetic materials.
4.Seals and Shields: Deep groove ball bearings can be provided with seals or protection to save them from contamination. Seals are normally made of synthetic rubber or other elastomers and form a barrier to stop dust, dirt, and liquids from entering the bearing. Shields, constantly made of metal, supply less security but are more appropriate for high-speed applications where minimal friction is required.
Uses a 6211 deep groove ball bearing
The 6211 bearing, belonging to the 6200 series, is a popular and versatile component in mechanical systems across various industries. With a bore diameter of 55mm, an outer diameter of 100mm, and a width of 21mm, it serves numerous purposes:
The 6211 bearing is extensively used in manufacturing equipment, conveyor systems, and pumps, where it reduces friction and ensures reliable rotational movement. Tractors, harvesters, and crop processing machines rely on these bearings for smooth operation in demanding agricultural environments. In automotive wheel hubs, transmissions, and engine components, 6211 bearings provide support and facilitate seamless movement.
They are used in appliances like washing machines and dishwashers, contributing to the smooth operation of various rotating parts.
6211 bearings are essential in electric motor assemblies, ensuring minimal energy loss and extending the life of the motor.
Purposes of 6200 Deep Groove Ball Bearing
Numerous home equipment, including refrigerators, fans, washing machines, and others, employ the 6200 bearings. They can offer dependable assistance and continue to operate steadily for prolonged periods.
A wide range of other industries, including construction, aerospace, and agriculture, also use 6200 learning. The 6200 bearing also satisfies the unique needs of these sectors.
A popular and extensively utilized bearing model in many different sectors is the 6200 bearing. It excels in a variety of high-speed, high-temperature, and high-load applications because of its exceptional characteristics and great performance.
Applications of 6805 Deep Groove Ball Bearing
The 6805 bearing is a 25 mm ball bearing with a range of rotary and industrial automation applications. The 6805 Deep Groove Ball Bearings are of the open kind. The raceway and protected row of the 6805Z ball bearings are single. The 6805 ZZ ball bearing has a single-row raceway and is side-protected.
More precisely, 6805 ball bearings are used in a variety of automation and industrial applications. Their purpose is to lessen friction during rotation and sustain weights. The grade 25 balls are equally loaded, and they revolve in tandem with the inner bearing race.
Unravelling the Inner Workings of Deep Groove Ball Bearings
Deep groove ball bearings represent a specific category of rolling element bearings, celebrated for their unique capacity to endure both radial and axial loads. These bearings are comprised of several essential components: an inner ring, an outer ring, a cage, and a collection of steel balls. Their ‘deep groove’ design delineates a distinctive raceway geometry, affording them the remarkable ability to accommodate a broad spectrum of loads and speeds.
Friction Reduction and Enhanced Efficiency
The hallmark attribute of deep groove ball bearings is their remarkable aptitude for friction reduction. Their design cleverly minimizes the contact points between the steel balls and the raceways, yielding diminished friction and energy dissipation. This reduced friction not only augments machinery efficiency but also significantly extends the operational lifespan of the bearings themselves.
Versatility Across Multifarious Applications
Deep groove ball bearings manifest their adaptability by finding applications across an extensive array of industries. From commonplace household appliances and power tools to heavy-duty agricultural machinery and vital automotive components, these bearings exhibit steadfast performance in diverse operating environments. Their capacity to shoulder both radial and axial loads renders them a sought-after choice for a multitude of applications.
Guarding Against Contamination: Shields and Seals
Deep groove ball bearings offer a formidable defence against contamination and facilitate ongoing lubrication through the integration of shields and seals. Shields serve as robust protective barriers, shielding against larger particles. Conversely, seals present a more comprehensive safeguard, effectively thwarting the ingress of liquids and minute particles. This pivotal feature renders deep groove ball bearings amenable to deployment in environments that range from pristine to highly demanding.
Materials Used in Deep Groove Ball Bearings
The performance and longevity of deep groove ball bearings depend on the materials used in their construction. Several materials are commonly employed in the production of these bearings:
Bearing Rings: The outer and inner rings are typically made from high-quality steel, such as chrome steel (AISI 52100) or stainless steel. Chrome steel offers excellent hardness, wear resistance, and durability, while stainless steel is preferred for applications where corrosion resistance is crucial.
Rolling Elements: Steel balls are the most common rolling elements in deep groove ball bearings. These balls are manufactured from chrome steel or stainless steel and are precision-ground to ensure consistent size and shape. In some specialized applications, ceramic balls, which offer lower friction and higher corrosion resistance, are used.
Cage Material: Cages are typically made from steel, brass, or engineered polymers. Steel cages are common in high-load applications, while brass cages are used when corrosion resistance is essential. Polymer cages are lightweight and have low friction properties.
Shields and Seals: Shields are typically made from steel, while seals are composed of rubber, synthetic materials, or a combination of both. The choice between shields and seals depends on the application’s requirements, with seals providing superior protection against contaminants.
Manufacturing Processes
Deep groove ball bearings are precision-engineered components, and their manufacturing processes are critical to ensuring their high quality and reliability. The production of deep groove ball bearings typically involves the following steps:
Raw Material Selection: The manufacturing process begins with the selection of high-quality steel or other materials that provide the necessary properties, such as hardness and wear resistance.
Turning and Grinding: The selected materials are turned and ground to form the bearing’s basic structure. The raceways, outer and inner rings, and the ball grooves are machined to precise dimensions.
Heat Treatment: Heat treatment processes, including quenching and tempering, are applied to improve the bearing’s hardness, strength, and resistance to wear.
Assembly: The individual components, including the outer ring, inner ring, balls, and cage, are carefully assembled. This assembly is crucial to maintaining the bearing’s tolerance and smooth operation.
Surface Finish: The bearing’s surfaces are meticulously polished to ensure low friction and smooth rotation.
Quality Control: Strict quality control measures, such as dimensional inspections and durability tests, are performed to guarantee the bearings meet the desired specifications.
Operating Principles:
Deep groove ball bearings are a fundamental component in various mechanical systems, enabling the efficient transfer of rotational motion and reducing friction. Understanding their operating principles and inner workings is crucial to appreciate their significance in a wide range of applications.
The core principle behind the operation of deep groove ball bearings lies in their design, which employs small steel balls positioned within a raceway structure. When an external force is applied to the inner ring of the bearing, these balls serve as rolling elements, moving smoothly between the inner and outer rings. This rolling action minimizes the contact between the rings, thereby significantly reducing wear and friction. This reduction in friction is critical for enhancing the efficiency and longevity of machinery and equipment, as it minimizes energy losses and heat generation.
Inner Working:
The inner workings of deep groove ball bearings involve intricate engineering and manufacturing processes. The inner and outer rings, for instance, must be meticulously machined to ensure they are perfectly round and flat. This precision is essential to maintain minimal clearance between the rings, enabling the smooth rolling of the balls. Any deviations in the shape or dimensions of these rings can result in uneven loading and premature wear.
Equally critical are the balls themselves, which are manufactured with a high degree of precision. These balls must be uniform in size and shape to ensure that they roll smoothly within the raceway. Any variations in ball dimensions can lead to uneven loading, reduced efficiency, and, ultimately, the failure of the bearing.
Material Composition:
Furthermore, the material composition of the balls and the rings is carefully chosen to provide the necessary hardness, strength, and durability. This ensures that the bearing can withstand the forces and stresses it will encounter during its operational lifespan.
Deep groove ball bearings find application in a multitude of industries, from automotive and aerospace to manufacturing and construction. Their ability to reduce friction and facilitate smooth motion is integral to the functioning of numerous mechanical systems, ranging from electric motors and conveyor systems to household appliances and more. In essence, deep groove ball bearings are a testament to the intersection of precision engineering and practical functionality, playing a pivotal role in the smooth operation of machinery and equipment across the globe.
Frequently Asked Questions (FAQs) Concerning Deep Groove Ball Bearings
What is a deep groove ball bearing, and how does it work?
A deep groove ball bearing, also known as a radial ball bearing, is a type of rolling element bearing designed to handle primarily radial and axial loads. It operates by using small balls that roll smoothly within deep, uninterrupted raceway grooves on the inner and outer rings, minimizing friction and enabling the transfer of rotational motion.
What are the main components of a deep groove ball bearing?
Deep groove ball bearings consist of several key components, including inner and outer rings, balls, cages (or retainers), and optional seals or shields. These components work together to enable smooth and reliable rotation.
What are the common materials used in deep groove ball bearings?
The outer and inner rings are commonly made from high-quality steel, like chrome steel or stainless steel. Steel balls are widely used as rolling elements, while cages can be made from steel, brass, or engineered polymers. Shields and seals are normally composed of steel, rubber, or synthetic materials.
What are the primary applications of deep groove ball bearings?
Deep groove ball bearings are used in a wide range of applications, including manufacturing equipment, automotive components, household appliances, electric motors, conveyor systems, and many more. They are essential wherever smooth and reliable rotational movement is required.
Are there different types of deep groove ball bearings, and how do I choose the right one for my application?
Yes, there are various types, including single-row and double-row deep groove ball bearings, with or without shields and seals. To select the right bearing for your application, consider factors like load, speed, operating conditions, and environmental factors. Consulting with a bearing specialist is often helpful.
What are the advantages of using ceramic balls in deep groove ball bearings?
Ceramic balls show lower friction and higher erosion resistance than steel balls. They are commonly used in high-performance applications where decreased importance and increased speed are important.
How are deep groove ball bearings manufactured, and what quality control measures are in place?
Deep groove ball bearings undergo a series of manufacturing processes, including turning, grinding, heat treatment, assembly, and surface finishing. Strict quality control measures are employed, including dimensional inspections and durability tests, to ensure the bearings meet specified standards.
What is the lifespan of a deep groove ball bearing, and how can I extend its longevity?
The lifespan of a deep groove ball bearing depends on factors such as load, speed, and maintenance. Regular maintenance, proper lubrication, and avoiding overloading can significantly extend the bearing’s longevity.
Can deep groove ball bearings be used in high-temperature or high-load applications?
Yes, deep groove ball bearings are versatile and can be selected with features suitable for high-temperature and high-load environments. Specialized bearing types and materials are available for these conditions.
Are deep groove ball bearings suitable for both industrial and domestic applications?
Yes, deep groove ball bearings are used in a wide range of applications, from heavy industrial machinery to everyday household appliances, due to their ability to provide smooth and efficient motion.
Final Thoughts
In conclusion, deep groove ball bearings are versatile and efficient components that play a crucial role in various industries and applications. Their ability to handle radial and axial loads while minimizing friction makes them indispensable in many mechanical systems.
These bearings consist of inner and outer rings, balls, cages, and optional seals or shields, all meticulously designed and manufactured to ensure reliable and smooth rotation. The choice of materials, including high-quality steel for rings and various options for rolling elements, allows for customization to suit different applications.
We discussed specific examples, such as the 6211 and 6200 deep groove ball bearings, highlighting their widespread use in manufacturing equipment, automotive components, and household appliances, among others. Additionally, we explored the application of the 6805 bearing in rotary and industrial automation contexts.
The manufacturing processes involved in producing deep groove ball bearings were also outlined, emphasizing the importance of quality control measures to meet specified standards.
Deep groove ball bearings are remarkable for their ability to reduce friction and enhance the efficiency and longevity of machinery and equipment. Their adaptability across various applications, from industrial settings to everyday household use, underscores their importance in modern engineering and technology.