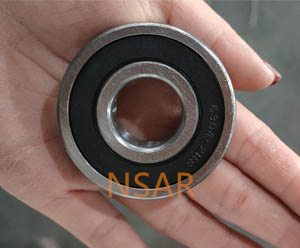
How to Make Ball Bearings
Material Selection:
The first step is selecting the appropriate materials for the bearing components. Common materials include chrome steel, stainless steel, and ceramics, depending on the intended application.
Cutting and Forming:
The selected material is cut and shaped into rough parts using various methods, such as forging, casting, or machining. This step forms the basic shape of the inner and outer rings.
Heat Treatment:
The rough parts undergo heat treatment to enhance their hardness, durability, and resistance to wear. This process involves heating the parts to a specific temperature and then cooling them rapidly.
Turning and Grinding:
The rings are precision-turned and ground to achieve the final dimensions. This step ensures smooth surfaces and tight tolerances necessary for proper bearing function.
Annealing:
The rings may undergo annealing, a heat treatment process that relieves internal stresses, improves machinability, and enhances the overall mechanical properties of the material.
Assembly:
Assembly involves fitting the balls and cages into the inner and outer rings. The balls are typically inserted into the space between the two rings, and a cage is used to maintain the ball spacing.
Riveting or Staking:
To secure the balls in place, the inner and outer rings may undergo a process called riveting or staking. This involves deforming a small portion of the ring material to trap the balls and prevent them from falling out.
Cleaning and Inspection:
The assembled bearings go through a cleaning process to remove any contaminants. After cleaning, they undergo rigorous inspection to ensure they meet quality standards and dimensional specifications.
Lubrication:
Bearings are lubricated to reduce friction and wear during operation. The type and amount of lubrication depend on the application and the operating conditions of the bearing.
Sealing:
In some cases, bearings are sealed to protect them from contaminants and retain lubrication. Seals can be made from various materials, such as rubber or metal.
Final Inspection:
The finished bearings undergo a final inspection to check for defects, verify dimensions, and ensure that they meet the required quality standards.
DFL Group is based on Hebei DFL Minmet Refractories Corp. Includes Hebei DFL Minmet Refractories Corp., Hong Kong CODO company, NSAR IND LLC in U.S.A., NSAR bearing manufacturing factory and a number of NSAR brand designated manufacturers. Our brands include NSAR, 3D, OWO, CBQ, and NASA .
NSAR bearings management team of managers, engineers, and technical staff have 15 – 25 years experience.
We supply customers with bearings not only produced in our own factory, but also produced in professional bearings plants designated by NSAR brand to meet customers’ different requirements, such as deep groove ball bearings,pillow block ball bearings,we have designated a factory in northern China, which has perfect testing equipment and can develop products to customer needs very rapidly. Miniature bearings are arranged in the factory in southern China, which has enjoyed a good reputation long term in producing miniature bearings.